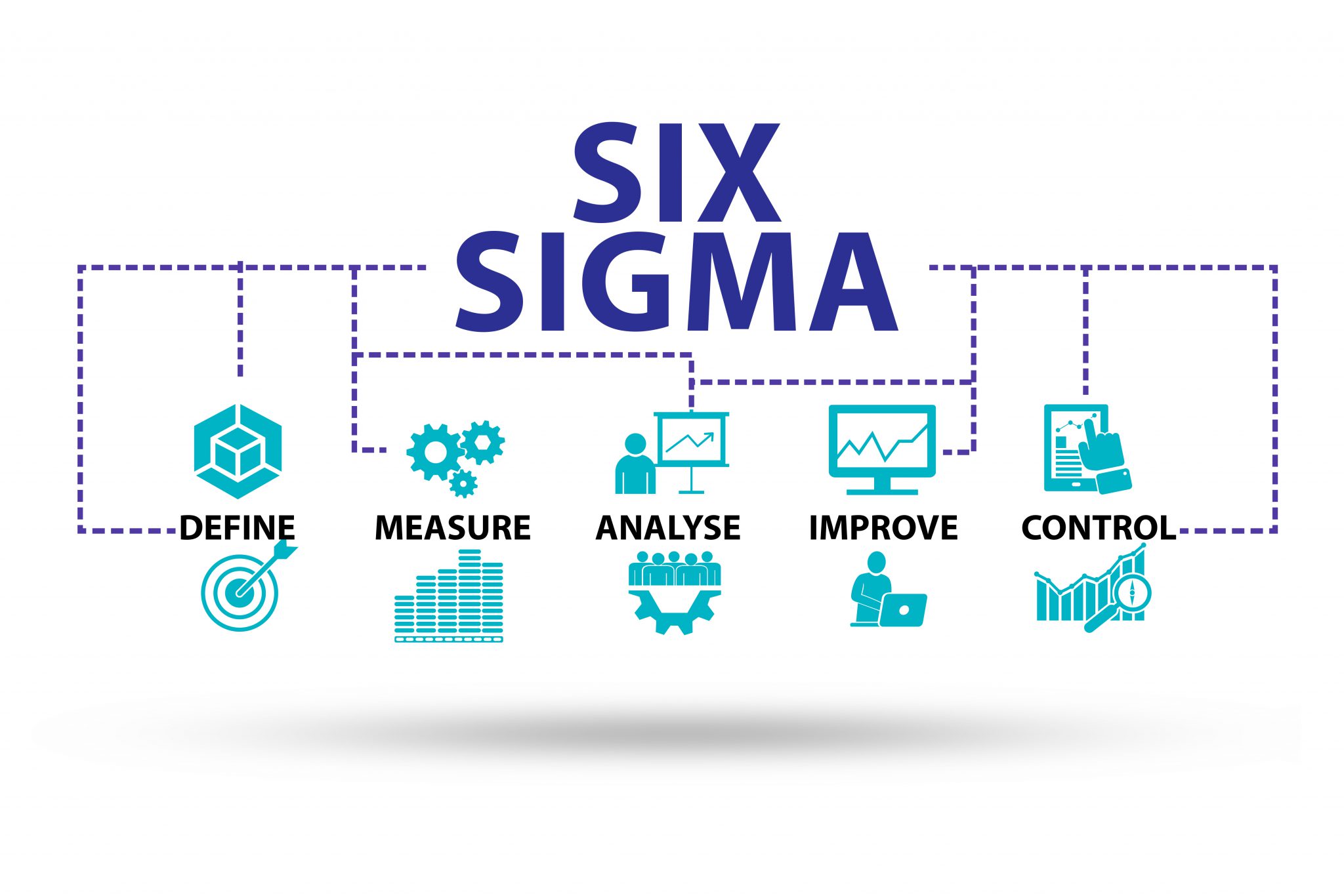
日本人だけが知らない、リーン/シックスシグマ
私は20年近く「リーン/シックスシグマ」のコンサルタントとして活動しています。リーン/シックスシグマとは何かを知らない方が大半だと思いますが、これは世界標準なのですが、日本では一時的に流行したものの、知らない/忘れ去ったという方がほとんどと思われます。
「リーン/シックスシグマ」は継続的な企業変革の方法論です。企業変革力・課題解決・継続的イノベーション・オペレーショナルエクセレンス・トランスフォーメーションといった単語に引っかかる方やシックスシグマを昔聞いたけど最近知らないという方に、ざっと目を通していただいて概略を理解していただけると幸いです。
なお、基本的に世間でリーン/シックスシグマと言うと大企業向けの方法論となります。しかしその考え方や手法などは中小~中堅製造業でも十分活用できます。
リーン/シックスシグマとは?
リーン/シックスシグマとは「企業変革の方法論」の1つで、語源はトヨタ生産方式を研究した「リーン生産方式」とGEが推進していたバラツキを抑えるプロセス改善の方法論「シックスシグマ」がくっついたものです。なんとも分かりやすく、当時世界最高のものづくり企業のトヨタと世界最高の経営をしていたGEのいいとこ取りをしたのです。なお、企業変革の方法論と言っているのは、単なる課題解決ではなく、財務効果を出しながらリーダー人材を育成することが目的とされるからです。
ちなみに、トヨタ生産方式もプロセス改善のシックスシグマも主にオペレーションの変革が得意な方法論であり破壊的イノベーションとは異なるので、たびたび「リーン/シックスシグマがイノベーションの邪魔をする」と海外で言われます。ただそれは、リーン/シックスシグマで継続的イノベーションを経験しているから言えることと思いますし、破壊的イノベーションと両立を考えればいいことで、リーン/シックスシグマの問題とは違います。
リーン/シックスシグマは主に欧米の大企業で取り入れられ、後ほど詳しく説明しますが、それが世界中にどんどん広がっています。日本ではソニー、東芝、島津製作所、LIXILなどの製造業や、星野リゾート、マツダ病院などのサービス業にも導入されています。世界では「世界標準」なので挙げるとキリがなく、例えば大手製薬や金融は日本企業以外ほぼ全部の企業で取り入れている状況です。
なぜリーン/シックスシグマを取り組むのか
世界中の企業が導入しているリーン/シックスシグマ。きっかけは後述のGEですが、なぜ続けたり新たに導入するか、簡単に整理します。
<リーン/シックスシグマの主な実施理由>
①経営課題を解決する共通言語を社内/取引先と持ちたい
②継続的イノベーションを行い、オペレーショナルエクセレンスを実現したい
③取引先など外部からの強い要求があった
④品質レベルを強化したい
①経営課題を解決する共通言語を社内/取引先と持ちたい
これが最大の特徴であり理由にもなります。最初何気なく社長のわがままみたいな理由でやり始めても、本格的に実施・継続する理由は「共通言語」です。
無手勝流の課題解決ではなく再現性がありノウハウを貯められる課題解決を社内の主要人物が身につけていて、しかも課題解決活動をマネジメントできると、ものすごく課題解決がスムーズに進むようになります。さらには取引先もリーン/シックスシグマを導入していることが多い海外では、社内だけでなく取引先と課題解決をすることもあります。
②継続的イノベーションを行い、オペレーショナルエクセレンスを実現したい
最近はあまり言われなくなっていますが、「オペレーショナルエクセレンス(Operational Excellence)」という経営戦略があり、それを実践することとリーン/シックスシグマはセットで考えられることが多いです。
オペレーショナル・エクセレンスとは、「業務改善プロセスが現場に定着し、業務オペレーションが磨きあげられ、競争上の優位性にまでなっている状態のこと(Wikipediaより)」を言い、プロダクト・イノベーション(革新的な製品)とカスタマー・インティマシー(顧客との圧倒的な親密度)と並ぶ重要な経営戦略と位置づけられています。
例えばDELLがオペレーショナルエクセレンスのいい見本です。卸などを通さずダイレクト販売し、BTO(受注生産:Build To Order)を素早く実施できる業務(オペレーション)を構築し、その他にもサプライヤーネットワークと業務を再整備などを行って、価格で圧倒的な競争力を持つようになりました。
DELLのような状態には一朝一夕にはなれません。だから競争優位に立てるのですが、その状態を作るために課題解決をこれでもかとやり続けるのです。そこで、課題解決の質とスピードを上げるためにリーン/シックスシグマを使います。
③取引先など外部からの強い要求があった
とあるクライアントから最近聞いた話ですが、海外で提携しようとした企業から「リーン/シックスシグマをやってないのか。ブラックベルト(課題解決リーダー)は何人いる?」と聞かれたそうです。結果的に「3年以内にシックスシグマをこのレベルまで持っていかないと次の契約延長はない」と言われて提携しました。
後述しますが、ISOを含めた各種規格でリーン/シックスシグマが求められるので強制力がありますし、取引先と共同で課題解決するのに共通言語がないと不便なので、海外では相手にリーン/シックスシグマを求めます。
外資系企業の日本法人から「本国からもっとちゃんとリーン/シックスシグマをやれ」と言われたので「英語のテキストなどは揃っているけど日本人は英語ができないから日本語で支援してくれるところを探している」という相談が多くあります。
海外では中小製造業でもリーン/シックスシグマを取り入れている企業が多くありますが、現在のように広まる前の導入理由は外圧が多かったです。有効活用できることがわかり、現在では普通に広く普及しています。
④品質レベルを強化したい
製造業が成長産業の国ではロバストな工程にするためにするため、リーン/シックスシグマが導入されます。製造業に限らず、例えば病院は業務品質を上げるために、金融は業務ミスを徹底して減らすために導入してきました。
元々リーン/シックスシグマは品質管理の方法論でした。冒頭から記述しているように今は違いますが、品質管理の方法論として有効なのは間違いないです。海外では戦略や自社の業務品質レベルに応じた使い方をしているイメージが強いです。
リーン/シックスシグマの7つの基本的な考え方
リーン/シックスシグマの7つの基本的な考え方を紹介します。
①顧客の利益に焦点を当てる
顧客の要求に焦点を合わせることが、リーン/シックスシグマの中で最も重要な考え方です。顧客の価値と需要を念頭に置いて課題解決が行われ、製品またはサービスのレベルを向上させます。プロダクトアウトにならない仕組になっています。
②データと論理的思考に基づいて科学的に課題解決する
課題に関する仮説を論理的に構築し、顧客やプロセスの事実とデータを収集して仮説を検証することを繰り返します。「急がば回れ」と言うことがありますが、確実に解決するために各種分析を行います。リーン/シックスシグマの語源にもなっている統計手法も使いますが、これは確実性を効率的に高めるためです。
③プロセスに着目する
プロセスの実態を確認し、プロセス上の問題のメカニズムと真の原因を追求し、新プロセスを構築します。私たちは「プロセス憎んで人を憎まず」と言いますが、人に依存しないプロセスを創ります。
④バリエーション(バラツキとムダ)とボトルネックを取り除く
バラツキを低減してロバストな工程を作る、7つのムダを省く、ボトルネックを改善してスムーズな流れを作る、という視点で改善します。特にバラツキは重要な考え方で、あらゆる場面、ツールで出てきます。
⑤DMAICを中核とした共通言語を用いる
同じステップ、同じツール、同じ用語をみんなが使うことにより、組織の課題解決能力が向上します。無手勝流だとどう解決されたかわかりづらいです。同じ方法であればノウハウの蓄積にもつながります。この共通言語という考え方は、企業変革力向上に必須の考え方です。
⑥トップダウンで課題を設定し、明確な責任と役割で解決する
経営戦略や課題をブレークダウンして取り組み課題を設定し、重要な取り組みとして本気でプロジェクトによる課題解決を行います。現場に転がっている課題のボトムアップで、現場任せの活動ではありません。経営上の重要な課題を確実に解決するために、責任と役割も明確にします。
⑦人を巻き込み、人を育てる
理屈では課題は解決せず、人が動いて始めて結果が出ます。変化に対して人は抵抗感を持ちます。巻き込んで成功することがリーダーに求められます。解決出来るようにリーダーを育て、メンバーを育て、関係者を育てます。育ったリーダーを次のマネジメントにして、人財育成のサイクルを回します。
リーン/シックスシグマは、リーンと2つのシックスシグマから出来ている
リーン/シックスシグマは、リーン生産方式、シックスシグマ、DFSS(Design for Six Sigma)の3つの課題解決の方法論から成り立っています。
①シックスシグマ
「シックスシグマ(6σ)」は統計学で「不良率を100万分の3.4以下にする」という意味です。それが昇華して経営改革の方法論として有名になりました。
そしてシックスシグマと言えばDMAIC。DMAICとは「Define:問題の定義、Measure:現状の測定、Analyze:原因の分析、Improve:改善策の立案、Control:改善実施と定着」のことです。当たり前のステップですが、ものすごく具体的かつ明確に体系化されています。
さらに各ステップごとに目的と成果物やツールが明確になっていることが特徴です。詳しくはこちらの記事をごらん下さい。
②リーン生産方式
「リーン生産方式」は、トヨタ自動車の生産方式である「TPS(トヨタ生産方式:Toyota Production System)」を研究し、体系として再構築した上で編み出された生産方式です。リーン(Lean)とは「ぜい肉の取れた、体が締まった、痩せた」という意味で、ムダのない生産方式と例えて名付けられました。
内容はほぼトヨタ生産方式と同じで、よりシステマティックにまとめられているだけと思ってください。ここでは2つの柱となる考え方だけご紹介します。
トヨタ生産方式は、「異常が発生したら機械がただちに停止して、不良品を造らない」という考え方(トヨタではニンベンの付いた「自働化」といいます)と、各工程が必要なものだけを、流れるように停滞なく生産する考え方(「ジャスト・イン・タイム」)の2つの考え方を柱として確立されました。
※トヨタ自動車HPより
シックスシグマとは異なるアプローチで、リーン生産方式は経験則の塊です。私はシックスシグマを基本に、テーマに合わせてリーン生産方式の考え方やツールを活用する形で「リーン/シックスシグマ」としています。
③DFSS(Design for Six Sigma)
「DFSS(Design for Six Sigma)」は、新製品や新サービス、新プロセスの設計開発専用シックスシグマです。 顧客の要求品質を徹底的に開発に組み込むもので、
DFSSはDMAICとは異なり、DMADVというステップになります。DMADVは「Define:課題の定義、Measure:顧客ニーズの測定、Analysis:基本設計、Design:詳細設計、Verify:検証」のことです。
プロダクトアウトにならないよう、顧客や市場をちゃんと理解し、それを製品仕様や技術仕様に落とし込むための方法です。なお、DMAICとDMADVの違いを整理したものが以下の図です。
世界の中のリーン/シックスシグマ
世界標準と冒頭から書いていますが、具体的にどういう状況か説明します。
まず、ISOで推奨規格ながらも2011年にISO13053、2015年にISO18404と正式採用されています。ISOは元々はヨーロッパ主体の組織で、ヨーロッパが正式採用したと言っても過言ではありません。シックスシグマのプロジェクトリーダーを「ブラックベルト」と言います。このブラックベルトは、イギリスでは国家資格となっています。
国家資格と言えば、先にブラックベルトを国家資格にしたのは中国です。ISO標準を開発するテクニカルコミッティという委員会がいくつかあるのですが、シックスシグマをISO化したテクニカルコミッティの当時の議長国は中国でした。そして韓国は国策として取り組んでおり、シンガポールでは「アジア リーン/シックスシグマ&プロセスエクセレンスサミット」が開催されるなど、アジア各国で取り組まれています。
シックスシグマの生みの親はモトローラで、育ての親はGE(ゼネラル・エレクトリック)と、米国育ちです。アメリカではamazonやシスコシステムズなどの圧倒的多数の代表的な企業で導入されています。官公庁、金融業など挙げるとキリがありません。
DHL(ドイツのグローバル物流企業)は、顧客企業と一緒にシックスシグマの方法論を使った物流費最適化プロジェクトをやっています。多国籍企業間で使われている方法論です。
「GE流で社風からITまで革新」、ジヤトコ秦社長、DHL山川社長らが講演
もう世界の先進国でリーン/シックスシグマを知らないのは日本だけです。
2020年度版ものづくり白書とリーン/シックスシグマ
2020年のものづくり白書をものすごくシンプルにまとめると「世界で不確実性が高まり、企業変革力の強化が必要。その強化をするためにデジタルトランスフォーメーションの推進が必要。」ということが書かれています。さらにデジタルトランスフォーメーションの内容を見てみると、AIやIoT、設計のデジタル化・デジタル連携の重要性が説かれています。
このAIとIoTや設計のデジタル化がシックスシグマと密接な関係なんです。AIとIoTは「データの収集→分析→(テクノロジーを使った)改善」を行い、その結果プロセスを競争力が高いレベルまで引き上げることが目的です。「企業変革に結びつくプロセス改善をデータを活用して実施する」はまさにシックスシグマなんです。設計のデジタル化も同じです。設計プロセスの品質を上げ、今後も挙げ続けるためのデータを「収集→分析→改善」します。デジタルと絡めて改善することが設計のデジタル化につながります。
シックスシグマの育ての親であるGEは、IoTプラットフォーム「Predix」を作りました。
GEジャパンのオンラインマガジン「GE Reports Japan」。グローバルな企業間競争や先進技術、企業経営や人材開発
発電設備や航空機エンジンでのノウハウを詰め込んでいますが、残念ながら事業としては上手く行ってないようです。しかしながら、発電設備や航空機エンジンのIoTのノウハウは素晴らしく、そのノウハウがシックスシグマによって作られてきたことは事実だと思っています。
ものづくり白書に書かれている事例などは、私はほとんどのものを自身のコンサルティングで経験しています。シックスシグマの中では当たり前のことで、それを白書で示す価値はあると思います。ただ、これを読んだ製造業の人で、まだデジタル化が進んでいない企業が「へー」で終わっていたら非常に危険だと思います。
世界は共通言語でもってIoTを進めています。またいつものようにガラパゴスで置いてけぼりにされる日本の姿が容易に想像できます。シックスシグマは元々は日本のTQC/TQMです。国としては体系化と共通言語化(日本流シックスシグマの敷衍)を進め、各企業は今後プラットフォームや規格に対応できるよう、シックスシグマを使った改善を進めるべきです。
リーン/シックスシグマの生い立ち
1980年代、ジャパン・アズ・No.1と言われていた時代に、アメリカが日本のものづくりを本気になって研究しに来ました。それがきっかけで、アメリカの携帯電話会社のモトローラのマイケル・ハリー博士が日本のTQC・TQMを徹底研究して方法論にしてシックスシグマが生まれました。当時は品質管理の方法論でした。
1990年代になり、GEがシックスシグマを始めます。ただし、GEは品質管理ではなく経営改革の方法論としてシックスシグマを活用しました。当時のGEのトップで伝説の経営者、ジャック・ウェルチ氏が持病である心臓病で入院したときに、経営判断を伴う改革が何も進まなかったことがきっかけでした。彼は企業変革を進めるリーダーを育てる必要性を強く感じ、「組織を巻き込んで再現性のあるやり方で成果を上げる」ことをシックスシグマで始めました。それが時価総額世界一の要因になったので、瞬く間に世界へシックスシグマが広がりました。
またリーン生産方式は、1990年にマサチューセッツ工科大学(MIT)のジェームズ・P・ウォマック氏とダニエル・T・ジョーンズ氏らが共同で研究して内容をまとめた著書「リーン生産方式が世界の自動車産業をこう変える」が出版されました。シックスシグマと同様に日本のものづくりを体系化したもので、トヨタブランドもあってこちらも同時期に全米に広がります。
2000年代からリーン/シックスシグマが出てきます。両方がアメリカで1990年代に広がり、2001年に「リーンシックスシグマへの傾倒:リーンエンタープライズとシックスシグマの統合への道」という本がアメリカで出版されました。ここからリーン/シックスシグマとしての道がスタートします。また2000年代には製造業以外の金融やヘルスケア(病院も含む)、サービス業にも広まりました。GE出身者が他の様々な企業で導入したので、世界中の様々な業種に一気に広がりました。
日本では、リーンはトヨタ生産方式として広まっていますが、シックスシグマは2000年代に流行して多くの企業が導入しようとしました。しかし数年でやめるところが多かったです。当時あまり共通言語や顧客と一緒に課題解決するような発想もなく、自社でQC活動をやっているところはピンとこなかくて本気になれなかったことが大きな原因だと思います。「TQCと何が違う」という質問は、色んなところでおそらく1,000回は聞きました。こんなところでも日本はガラパゴスになっていたのです。
そして2010年代以降は上に書いた「世界の中のリーン/シックスシグマ」に続くことになります。